PEX Guide: What is operational excellence?
Discover what true operational excellence means and the methodologies and technologies companies should adopt for successful business outcomes
Add bookmarkListen to this content
Audio conversion provided by OpenAI
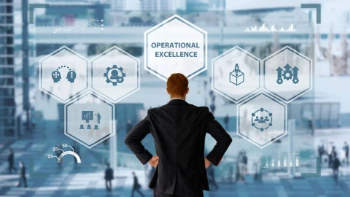
This PEX Network guide explains what operational excellence is, along with the methodologies and technologies companies can adopt to improve business operations and deliver successful outcomes.
Featuring real-life case studies and recommendations from organizations including LEGO, Coca-Cola and LiveNation, this guide outlines how businesses can optimize their processes to improve efficiency, cut internal costs and improve customer experience.
By the end of this article, you will have a thorough understanding of how operational excellence can help businesses big and small deliver strategic objectives and manage growth, even during challenging times.
Don't miss any news, updates or insider tips from PEX Network by getting them delivered to your inbox. Sign up to our newsletter and join our community of experts.
Contents
- What is operational excellence?
- How does operational excellence benefit businesses?
- The key methodologies for achieving operational excellence
- The technologies that enable operational excellence
- The importance of people and culture
- How to measure operational excellence
- Operational excellence in action: real-life case studies
- The future of operational excellence
- Further resources
What is operational excellence?
Operational excellence is an approach that aims to make an organization's processes more efficient. Its ultimate goal is to ensure customers' expectations are met, while the company's operations are continually improving.
Peter Evans, director of service and performance management for shared services at LEGO, says that “Operational excellence is about the journey that you are working with the business on, which means you must have an understanding of the whole business holistically.”
“You don't deliver a culture with nice PowerPoints, you deliver a culture by everybody working together and understanding the why of what we're doing. Through connecting what we do in terms of the services we deliver to excellence for what we want to achieve."
Peter Evans, director of service and performance management for shared services at LEGO
Operational excellence is often used interchangeably with process excellence, however, it is not the same concept.
How does operational excellence benefit businesses?
The purpose of achieving operational excellence is for a business to operate as efficiently as possible thanks to optimized businesses processes, full visibility across departments, and a company culture that supports continuous improvement and process changes.
Brenton Harder, head of automation at Fiserv explains: “Companies with operational excellence know where they are excellent because they have the right measures and pulse points to know whether they are improving or not. They have visibility through their data of the way they work.”
The key methodologies for achieving operational excellence
There are several methodologies that enable organizations to understand and optimize their internal business processes. The choice of methodology will depend on the specific needs and goals of the organization.
Continuous improvement is an ongoing effort to enhance operations
As its name suggests, continuous improvement is an ongoing effort to enhance business processes, services and products. This approach encourages employees at all levels to identify and implement process improvements continuously, in the belief that there is always room for improvement regardless of how well a current process is performing.
Process failure mode effects analysis reduces risks
Process failure mode effects analysis (PFMEA) is a structured analytical tool that can be used by a whole organization, business unit or cross-functional team to establish the impact of a process failure, and identify and prioritize actions to reduce risks.
PFMEA is a living document that should be created before production, and maintained throughout the lifecycle of a product.
Lean helps businesses remove waste
The Lean methodology is a philosophical way of working focused on removing waste to achieve process and operational excellence. Its goal is the removal of anything that does not add value for the end customer, with the value being any action or process that a customer would be willing to pay for.
Read more: What is Lean?
There are seven forms of waste according to the Lean approach, identified by Toyota chief engineer Taiichi Ohno. These are: overproduction, unnecessary transportation, excessive inventory, excessive motion, defects, over-processing and waiting.
Although not part of Toyota’s original list, an eighth waste exists within organizations: non-utilized talent. Together, the eight wastes of Lean make up the acronym DOWNTIME.
Six Sigma uses data to reduce errors
Six Sigma is a customer-centric methodology that uses a data-driven approach to reduce defects by eliminating variations and errors. Any process output that does not meet customer specifications is seen as a defect and is removed through one of two approaches: define, measure, analyze, improve and control (DMAIC) or define, measure, analyze, design and verify (DMADV).
Lean Six Sigma removes waste and improves efficiency
Established in 1986 by staff at Motorola, Lean Six Sigma combines Lean and Six Sigma approaches to reduce waste and increase efficiency while minimizing defects and improving quality at the same time.
Business process management maps opportunities for development
Business process management (BPM) is an evolving management discipline that has been around for more than 30 years. It allows organizations to analyze and map out their internal end-to-end processes to find opportunities for improvement.
This can involve the execution, control, modelling, measurement and optimization of business activity flows. It often helps organizations identify opportunities for process automation.
“At the end of the day, what BPM does is formalize business requirements, including implementing any potential technologies, reengineering processes and facilitating change management.”
Giovanni Angeli, senior manager BPM, IT strategic business solutions at Coca-Cola European Partners
Total quality management (TQM) prioritizes the customer
A customer-focused approach, total quality management (TQM) emphasizes continuous improvement, employee involvement and leadership commitment to quality. By making customer needs the priority, its goal is to achieve greater efficiencies, lower operating costs and increase market share.
Theory of constraints (ToC) removes processes that limit operational goals
This philosophy focuses on identifying and removing constraints in a business system to improve overall flow and efficiency. A constraint is defined as any process that limits the ability of an entire system to achieve its intended goal.
Read more: Four ways to combine six sigma with theory of constraints
Change management enables business transformation
Although not a methodology in itself, change management is an important tool in the world of operational excellence. As organizations transform, change internal processes and implement new technologies, it is crucial to constantly communicate these changes, train employees and receive feedback from across the organization to measure the success of adoption.
There are several steps to successful change management: determining the aspect of the business that needs improvement, ensuring cross-organizational buy-in, planning, readiness and data management, implementing change, and reviewing efforts.
The technologies that enable operational excellence
There are various technologies that can help organizations streamline their processes, reduce costs and improve customer experience to reach the ultimate goal of operational excellence.
Business process management software provides a holistic view of processes
While BPM is primarily a methodology, there are three types of BPM software platforms that can help speed up application development, business processes remodeling and digitization. A basic BPM platform is a controlled repository of an organization’s standard operating procedures and documentation.
Going further, a BPM suite features a structure providing a holistic view of all processes and an understanding of the interdependencies between all departments involved. An intelligent BPM suite will allow BPM teams to design a new process and simulate it to understand its impact on an organization.
Robotic process automation can reduce time spent on manual repetitive tasks
Robotic process automation (RPA) is a technology that uses software robots to imitate human execution of a business process. It is primarily used for manual repetitive tasks that are prone to error, such as manual data input, or processes that take time away from other tasks that bring more value to the business.
There are different types of bots that meet different business needs. Some can be programmed according to set parameters, while others use artificial intelligence (AI) to analyze data, learn how employees complete a process, and then perform that process itself.
Process mining collects data to create business intelligence
A lack of visibility over what is happening in business processes limits the organization's ability to implement process improvements, as there is no accurate way to determine where they are necessary. Process mining offers a solution to this, as it collects, stores, analyzes and links process data together.
Process mining software gives organizations an overview of business processes by collecting relevant data. This data is then turned into business intelligence and actionable insights on ways to improve processes and work towards operational excellence.
Learn more about how to convert data into actionable insights in this podcast with Vartul Mittal, digital transformation leader at Barclays and technology council member at Forbes:
As it only focuses on systems that produce logs, this is where process discovery can help, as this software collects data on all employee behavior anonymously on systems not covered by process mining, such as Excel sheets.
Intelligent automation combines technologies to resolve issues
Organizations that are mature in their RPA journey can take the intelligent automation (IA) approach to support operational excellence. Combining BPM, RPA, process mining, data analytics, AI and machine learning, IA allows organizations to observe, analyze and map out internal business processes.
“Organizations need to orchestrate the technologies brought in so they can be executed to resolve issues, otherwise time and money are wasted.”
Laxmikant Pukale, director of intelligent automation at USAA
Hyperautomation provides enhance visibility of business processes
Going beyond intelligent automation in an organizations’ RPA journey, hyperautomation is the orchestration of all intelligent automation technologies that have learned to be autonomous to decide which processes are best to automate.
Hyperautomation provides a full business overview with advanced real-time analytics and control of the entire automation lifecycle. It can lead to the creation of a digital twin to allow organizations to simulate changes to processes.
Low-code enables development without coding experts
A low-code approach to these technologies enables organizations to develop and implement custom applications quickly without requiring coding experts to do so. Deploying this approach can save businesses substantial amounts of time and effort.
The importance of people and culture
In PEX Report 2023: Global state of process excellence, survey respondents identified that creating a culture that enables organizational transformation will be a top priority for the 12 months ahead.
Businesses must engage employees to drive operational excellence and any meaningful transformation program, through continuous learning, upskilling, professional development and retention.
A good example of this is implementing low-code and no-code programs that enable employees at all levels to develop solutions and experiment with them.
"By developing a culture of process excellence, businesses can imbue their staff with a sense of ownership and engagement that encourages a great organizational culture beyond the way operations are handled," says Thomas Kohlenbach, senior product specialist at Nintex. "As confidence grows and people see that their part in the business is valued and meaningful, everybody wins."
How to measure operational excellence
There are various ways to measure operational excellence, however to do so effectively organizations must set realistic targets and remain committed to them. A combination of key performance indicators can be used, including:
- Customer satisfaction. Measured through customer surveys, Net Promoter Score (NPS) and other ways to gather feedback from the end customer.
- Process efficiency. Assessing whether metrics such as cycle time, lead time and error rates have improved can help measure the efficiency of key processes.
- Cost reduction. This includes assessing the cost per unit, total cost of ownership and return on investment (ROI).
- Employee engagement. Employee surveys can be used to measure levels of employee satisfaction within an organization and whether staff are engaged in operational excellence initiatives.
- Six Sigma Define, Measure, Analyze, Improve, Control (DMAIC). This framework can help identify opportunities for improvement and measure the results of improvement initiatives.
Operational excellence in action: real-life case studies
PEX Network has gathered a number of operational excellence success stories in a wide range of industries including financial services, healthcare and retail. We have included a selection of these here.
Achieving operational excellence in the financial sector
At US-based credit union service organization PSCU, the focus on achieving operational excellence has been primarily on lean internal development. The business has launched a grassroots campaign teaching Lean Six Sigma to front line employees. Additionally, its Center of Process Excellence (CPE) has developed a belt training program starting with yellow belt, both in person and virtually.
The CPE consisting of certified black belts and master black belts focuses on cross-functional organization-wide initiatives where lean techniques and process maturity assessments are encouraged.
Driving process excellence in a merger
Following the merger of Hitachi Vantara and Hitachi Consulting in January 2020, Dr. Tobias S. Witte, director of the global project management and business process excellence, had the objective of bringing people, systems and processes together. His main goal was to define standard processes through a BPM program and streamline a connected IT environment.
To reach this objective, he had three main tasks. Firstly, merging IT systems to create an ideal, scalable IT environment. Secondly, to capture process synergies between the former separate companies to increase the organization’s efficiency. Thirdly, to combine the offerings of the two companies and combine them to cross-sell, solve clients’ business challenges and drive profitability.
Covid-19 and the need for process automation
At global music management and promotion company LiveNation, the need to implement a process that ensured GDPR compliance led its BPM team to discover opportunities for process automation. This resulted in the development of an internal RPA team halfway through 2020 tasked with exploring processes that would be more effective if automated.
The company’s refund process in particular had to be automated due to the huge demand on its operational functions. Before automation the process involved one ticket at a time being refunded by a human worker from a call center via a legacy system.
How RPA reduced process time length from 40 hours to 40 seconds
As a NetSuite solution user and provider, the Vested Group specializes in consulting, implementation, support and development of a full range of NetSuite products. Every six months, NetSuite has a new product release and all customers are required to test and validate that all functions work prior to going live. Failure to do so could increase the risk of downtime.
Understanding which functions needed testing would take a minimum of 40 hours per release per customer to complete. The length of testing time often resulted in organizations not fully testing their software, which increased the risk of a new feature not working.
After implementing RPA, the Vested Group reduced checking time down to 40 seconds, dramatically saving labor time and decreasing risk for both them and their clients.
The future of operational excellence
The emerging trends of recent years are likely to continue shaping operational excellence in the future. Digital transformation, along with the adoption of technologies such as AI, machine learning (ML), augmented reality (AR) and automation, will continue to play a vital role in the way businesses optimize their processes.
As an example, AR can be deployed to help reduce errors and improve productivity by providing workers in manufacturing or assembly lines with information overlaid onto the equipment they are using, by wearing AR goggles. The technology can also be used for training and for remote collaboration in interactive environments.
However, as PEX Network's editor Elizabeth Mixson notes, while tools like automation and data analytics are important enablers for operational excellence, organizations sometimes go overboard. "Too much data can be just as useless as too little."
"Over-automating and over-engineering processes can increase inefficiencies. The key is finding balance between the human and technological elements."
Elizabeth Mixson, editor at PEX Network
There will be an increasing focus on sustainability as companies aim to reduce waste, for the dual purposes of working more efficiently and cost-effectively while minimizing their environmental footprint. Furthermore, an increasing number of business leaders believe that sustainability and process optimization go hand-in-hand when it comes to creating efficiencies and long-term growth.
Last but not least, remote working has emerged as one of the most transformative aspects for businesses worldwide of the last few years, a fact that is unlikely to change in the near future. Organizations must continue adapting to working in virtual environments by developing new approaches to collaboration, communication and process improvements.
Further resources
- How to unlock operational excellence with data
- The changing landscape of process excellence
- Why low-code platforms could be the new normal
- Chart your path to operational excellence in 2023
To get more industry guides like this delivered straight to your inbox join the PEX Network community here.
This article was originally published on April 8th, 2021 and updated on February 1st, 2023.
The 26th Annual OPEX Week: Business Transformation World Summit | post show report
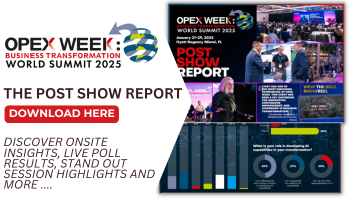
Over 550 transformation leaders from 200 companies across 17 countries gathered to share innovations and stories at OPEX Week 2025. The three unforgettable days sparked groundbreaking ideas and invaluable connections. Don't worry—we've got you covered with a full recap of the 2025 OPEX Week. Download the post-show report here.
To view this content, please fill out the form to register and become a member.
Or, if you're already a member, sign in below to view.
Please note: That all fields marked with an asterisk (*) are required.