Driving workplace safety and hygiene through AI gesture recognition
A new use case for AI driven by Covid-19 hygiene and safety requirements can improve future applications of the technology for process optimization
Add bookmark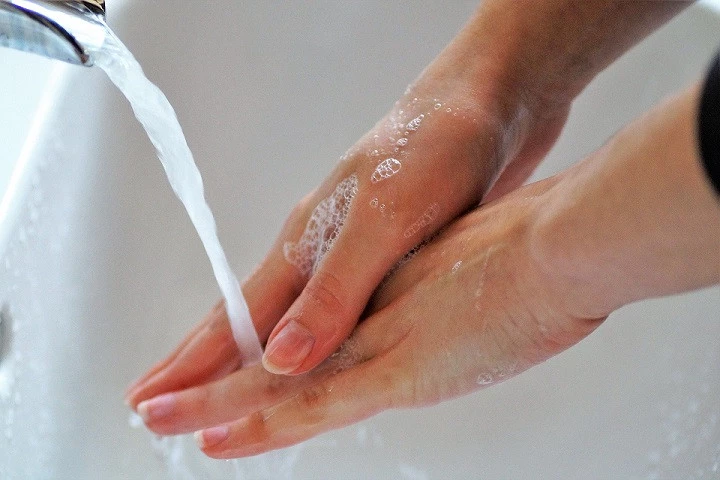
As the quest for process excellence enters a new decade, the state of technology in the field is more advanced than ever. Artificial intelligence (AI) has already been applied in state-of-the-art process improvement initiatives and the benefits it can provide are numerous, such as the speedy analysis of large data sets, process automation and implementation of predictive analytics. As the Covid-19 pandemic drives innovation, a unique application of AI for processes has emerged for organizations attempting to remain competitive during a period of commercial uncertainty.
Fujitsu Laboratories Ltd., a Japanese information and technology provider, recently announced the development of Actlyzer hand wash movement recognition technology. This is an expanded function of what was initially a behavioral analysis technology rolled out in Japan in 2019, which utilizes AI and machine learning to recognize a variety of simple and complex human activities in order to detect suspicious activity and track product interest. The current health crisis spurred Fujitsu Laboratories to develop a new use case for the technology, focused on improving workplace hygiene and safety.
Food and beverage organizations in Japan are preparing for new hygiene regulations which came in to play in May and there is a demand for a non-invasive method to confirm if employees have washed their hands as a safety measure against Covid-19.
The Actlyzer movement recognition technology has been developed to detect if an individual has washed their hands correctly as per the six-stage hand-washing process recommended by the Japanese Ministry of Health through gesture recognition. The traditional inspection procedure is manual and involves check sheets, self-reports and visual examinations by supervisors, which is far from ideal as a result of human error and the need to hire and provide resources for inspectors. As many organizations in the food and beverage industry move toward automation through machine learning to optimize their processes, these hand-washing checks present a significant opportunity to reduce cost.
Automation is one of the most prominently discussed methods for optimizing processes, as the return of investment has been justified time and again. Some organizations have been able to achieve as much as 3,800% return on investment in five months through AI, making it likely that industry uptake of technologies such as Actlyzer will increase in the coming years.
Organizations which embrace this advancement in AI technology will have the opportunity to free up considerable amounts of resources and improve their process efficiency, helping them to gain a competitive edge.