Impacting businesses’ top and bottom lines by optimizing procure-to-pay
With many global supply lines experiencing massive impairments, learn how process mining can uncover the root cause of delays and disturbances
Add bookmark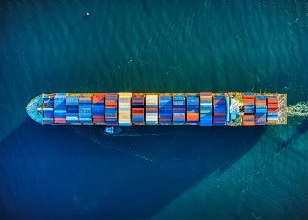
In many industries, problems in global supply chains lead to massive impairments in the ability of companies to deliver and compete. This article illustrates how process mining technologies can be used to optimize procurement processes and achieve supply chain resilience.
Due to the crises of recent years, global supply chains are threatened in a way they have rarely been in the last decades. Surveys of industrial companies show that complaints about bottlenecks and problems with precursors and raw materials are at an all-time high. Almost all industries are affected by shortages of raw materials.
As an example, the shortage of semiconductors and chips is particularly noticeable in consumer electronics and among car manufacturers and their suppliers. As another example, the increased demand for wood has ensured that this raw material is now considered a scarce commodity.
The associated costs and the lack of delivery capability have a direct impact on both the bottom and the top line of companies. Thus, the entire procurement system is moved into the center of the consideration.
A number of studies highlight the potential that lies in optimizing procurement processes:
- In a study by McKinsey, 81 percent of companies agree or strongly agree that procurement will need to reimagine its operations. McKinsey estimates a savings potential of 5 percent of the annual procurement volume.
- Bain & Company estimates in a March 2022 study that more than 60 percent of the total value of procurement stems from operational efforts.
- According to the Digital Procurement Survey 2022 by PwC, companies plan to invest an average of €1.28mn (US$1.35mn) in the digitalization of their procurement processes.
Optimization requires analyzing purchasing processes in detail to identify weaknesses and initiate improvement measures. This is a typical application area of process mining.
At first sight, procurement represents itself as a relatively simple operational sequence: a requirement request is provided, examined and transferred into a procurement order. After delivery by the selected supplier, the commodity and the calculation are examined and finally the invoices are paid.
It turns out, however, that a high degree of complexity is caused by the fact that there are very many variants and deviations that complicate, increase the cost of and slow down operational processing:
- Alternative offers from suppliers are often not directly comparable.
- Requisitions are rejected and revised before an order is generated from them.
- Delivery delays occur in manufacturing or transportation or orders are split into multiple deliveries.
- Inspection upon receipt may reveal quality problems that require returns.
- Invoices are disputed and paid only after modification.
All these examples lead to repetition and multiple work and this operational complexity increases both procurement costs and lead times. Supply chain planning is a complex process that involves a phenomena known as the 'bullwhip effect', leading to inventory shortages and oversupply in the wrong places.
Process mining leverages digital fingerprints and enables all procurement processes to be fully analyzed, both in terms of the structure of the flow and the resulting KPIs. On the basis of the process data, intelligent algorithms for root cause mining make it possible to reveal the causes and correlations of delivery problems and process deficiencies, and to initiate optimizations.
Here is more information on how to perfect your procure-to-pay operations with process mining
Beyond the corporate boundary, many companies are now trying to have production take place closer to the point of sale in order to counter delivery bottlenecks. Another possibility, especially in the direct-to-consumer sector, is to build up a warehouse yourself or to use the services of third-party logistics companies, thus enabling e-commerce brands to focus on their core business.
It is also true that the entire supply chain network is at the center of regulatory requirements. The supply chain act passed in Germany that comes into force on January 1, 2023, provides for the first time regulation on corporate responsibility for human rights compliance in supply chains, among direct suppliers and across hierarchies.
Core elements of the due diligence requirements include the establishment of risk management to identify, prevent or minimize the risks of human rights violations and damage to the environment. Fines can be up to €8mn or up to 2 percent of annual global sales. The EU commission has announced that it will issue an even stricter directive.
Monitoring is also essential with regard to these compliance requirements. Process mining makes it possible to monitor the specific execution for each procurement process and to compare it with the applicable regulations or to immediately object to violations.
In our global, networked economy, resilient and responsive ecosystems are replacing value chains that were previously fragmented or opaque. To strengthen global connectivity, minimize risks and increase resilience, companies must not only make their own operations more transparent, but also those of their trading partners.
Do you agree that global supply chains are facing an unprecedented level of threat? Let us know in the comments below.