Nokia’s approach to end-to-end digital process automation
How a bottom-up approach helped automate the customer purchase order process, saving time and internal costs
Add bookmark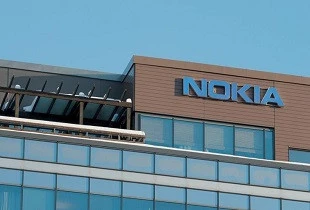
Finnish telecommunications company Nokia has undergone a multi-year digital transformation program on its supply chain and procurement processes.
PEX Network caught up with Katherine Dillon, automation process analyst and automation developer at Nokia, ahead of her presentation at PEX Live: Digital Process Automation and Low-Code 2021 to discuss her company’s end-to-end digital process automation (DPA) journey and her views on the current state of the market.
You can attend Dillon’s presentation by registering for PEX Live: Digital Process Automation and Low-Code 2021 here.
PEX Network: In your opinion, why do you think it is important for businesses to automate?
Katherine Dillon: Without automation, businesses today will not be able to meet performance requirements of the future, and transformation is needed. Businesses need to pursue strategies that will reduce costs, save time and increase efficiency and productivity. They can do this by utilizing automation tools, whichever fits best for the particular process or procedure they are trying to automate.
PEX Network: Which processes were Nokia’s focus for automation and why?
KD: We primarily focused on processes in supply chain and business operations. We noticed a large volume of manual transactions in our customer purchase orders (PO) for instance. By implementing automation into the workflow we were able to obtain detailed transactional data that we did not have before. Along with alleviating some of the manual tasks, we were able to increase our productivity and efficiency. It freed time for employees to concentrate on the more complex PO issues.
PEX Network: What motivated Nokia’s decision to automate end-to-end internal processes?
KD: As with any company, some of the top reasons for Nokia to automate is to improve efficiency and reduce cost, so a good place to start was looking at processes that are high in volume and/or high in manual tasks.
By implementing automation into the workflow we were able to obtain detailed transactional data that we did not have before, especially within a large portion of our manual tasks. In essence, it is the reason our team helps to digitalize our processes, to have that transparency.
PEX Network: What was your approach in deciding which processes to automate?
KD: When we started automating, we decided a bottom-up was a good approach. Our department leads wanted to find digitalization and automation opportunities and encouraged all team members to look for them. This enabled them to look at their own processes and recognize the manual tasks that could be automated.
From a high level you would not notice how many manual tasks need to be done at the working level of a process. By doing the bottom-up approach we were able to capture early on in our automation development journey some processes that might have gone amiss if we went with only a top-down approach.
“Full DPA will not be possible until every process can be captured and optimized in business infrastructure.”
Katherine Dillon, automation process analyst, automation developer at Nokia
PEX Network: How do you think the digital process automation market is, or should be evolving?
KD: I have noticed that one of the major impediments to a full end-to-end DPA is its integration into established business ecosystems. We need a tool to function on a high level to a macro level. It needs to be able to look at high-level procedures and also be able to drill down and capture the macro level.
It is sometimes at those macro levels that you can find ways to automate which in turn flow back up into the full end-to-end DPA system. Full DPA will not be possible until every process can be captured and optimized in the business infrastructure.
PEX Network: What development do you see in the digital process automation space over the next few years?
KD: I see a stronger focus on data management, quality and integration. It will leverage the implementation of machine learning and artificial intelligence to allow business processes to be optimized on a productive and prescriptive level.
I am talking about both structured and unstructured data. When you are implementing DPA you are able to see the processes that you have digitalized and hopefully have a marker to indicate that there is no automation past a certain point.
The goal is to get all processes automated, even though you will never fully eliminate manual tasks. At least everybody across all the silos will be able to see the full process from end-to-end. When making decisions to automate or improve a process down the line, they will be able to see how that process might affect all the individuals before it got to them. I believe this is very important in the coming future dealing with DPA space.
PEX Network: What key takeaway do you expect attendees to learn from your presentation at PEX Live: Digital Process Automation and Low-Code 2021?
KD: Automation is a continuous enhancement and not a “set and forget” methodology. The goal is to have the data to enable dynamic changes in operating models and procedures from end-to-end.