Three extraordinary examples of digital technology in action
Learn how Tata Steel, EC&R and Emirates Team New Zealand have created unique use cases for artificial intelligence, IoT and data analytics
Add bookmark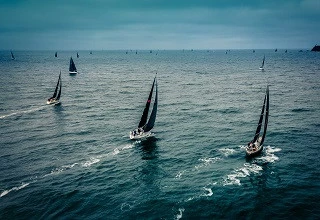
Businesses today are applying many varieties of digital technology to overhaul organizational processes. These technologies range from simple data management platforms to complex artificial intelligence (AI) augmented with machine learning.
There are many and varied applications of such technologies. This article looks at three unique examples of digital technology being applied to optimize processes.
Applying AI to win a major sporting event
June 17, 2021 saw the beginning of the America’s Cup, a competitive sailing event which offers the world’s oldest international sporting trophy. The 36th edition of this event held a key difference to all of the previous editions as a new element was at play. The defending champion, Emirates Team New Zealand, had added a new crew member: an AI bot developed by McKinsey.
The team had previously used a simulation program to test boat designs without ever having to build them, maximizing its ability to optimize that process ahead of the competition. The simulation required a human operator who could only test one boat design at once, which severely limited the amount of them that could be tested due to the sailors’ busy schedules.
Related content: Develop your data analytics and AI skills
The AI bot has the capacity to run thousands of simulations at once, taking the efficacy of the process to an unprecedented level. The bot was even trained to test the boats the way a professional sailor would using a relatively new approach called deep reinforcement learning, a derivative of machine learning.
The bot eventually became so skilled that the team was even learning new maneuvers from it, meaning that the bot is essentially a pioneer in the world of sailing. The result was a craft that had been designed from bow-to-stern with efficiency and performance in mind, a crew that had been trained with the power of AI and a victory for Emirates Team New Zealand.
Superheating steel with data
In the production of steel, it is necessary to ‘superheat’ the metal to a specific temperature before casting it. If the steel is heated too much or too little it will not be viable for casting and with an optimal temperature range of only 15 degrees Celsius, getting it right can be very tricky.
Tata Steel’s plant in Kalinganagar, India, would successfully complete the process two out of three times when it was conducted entirely based on worker experience. Managers saw an opportunity to improve this process and, consequently, increase profits. A centralized data platform was implemented along with advanced sensors to inform on the process.
Related content: Why companies should move away from manual process discovery
Initially, the production model developed through the new data platform, aimed at maximizing operational visibility, promised a success rate of 75 percent, which was an improvement. Employees were extensively trained in various areas of data analytics to improve their capabilities with the new platform which collates and analyzes plant data before it was rolled out.
Once operational, the platform provided recommendations to workers to improve their success rate for the superheating process. Initially there were some issues due to variety in customer orders, meaning operators rejected recommendations from the platform. The new data gathered along with further training for staff allowed them to further develop the approach.
Related content: Unlock operational excellence through data
The result was a model which predicts a 90 percent accuracy rate for the process, with employees now accepting 85 percent of the model’s recommendations. This has resulted in annual cost savings of US$4mn and the factory being recognized by the World Economic Forum for its digital capabilities.
Achieving a 20 percent profit increase with the Internet of Things (IoT)
In 2013, E.ON Climate and Renewables (EC&R) North America was operating with a 30 percent deviation margin with regard to predicted energy output. The business also calculated a 10 percent annual revenue loss due to overestimating wind conditions, both of which were extremely unfavorable.
Related content: Overseeing the wind of change in business
In an attempt to improve these statistics EC&R implemented a platform which utilizes the IoT to analyze tens of thousands of data points on a wind farm each second. The platform connects data from an array of sensors reporting on everything from operational and configuration data to mechanical load analytics and energy prediction.
Related content: Overcoming inefficient workflows in manufacturing
The enhanced, real-time visibility the platform offers has allowed for huge optimizations in energy output. In just the first year EC&R reported a 4 percent increase in annual energy output. By 2016, after having installed the IoT in more than 1,400 turbines, the business reported a 20 percent increase in annual profits.
Has your business developed an innovative application for digital technology? Let us know in the comments below.