Process lessons from a Formula 1 pit crew
How standardized and specialized processes can drive efficiency and excellence
Add bookmark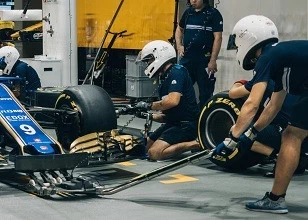
In November 2019 the Red Bull Racing team set the current world record for a Formula 1 pit stop at 1.82 seconds, during the Brazilian Grand Prix. That means changing four tires and adjusting the aerodynamics on a $10 mn supercar faster than most of us can access our smartphones or sign our names. That kind of performance does not just happen naturally.
Formula 1 teams drill hundreds of times and analyze every aspect of the pit stop action in order to perfect every step of the process that could make the difference between a podium finish and a difficult conversation with their sponsors.
Don't miss any news, updates or insider tips from PEX Network by getting them delivered to your inbox. Sign up to our newsletter and join our community of experts.
Know what you are doing
Pit crews drill until their actions are second nature and each of those actions is carefully prescribed. Everything is scrutinized, from the activities of the crew to the equipment they use. Not so long ago, each ”gunner”, meaning the crew using pneumatic wheel-nut guns to loosen and tighten the wheels, would raise their hands to indicate that they had completed their task.
The chief mechanic would scan for four hands in the air and then give the jack crew the go-ahead to drop the car so the driver could reenter the race. Today, each gunner has a button on their gun that indicates they have affixed the wheel, and when all four have been triggered, the jacks automatically disengage and the light goes green. Eliminating one action and the reaction time it took for someone to recognize it saved a considerable amount of time.
Consider how well you know your processes. What tasks are completed in order to move a product or data through each step? Which systems are implemented and where do they connect? What actions do your team members take at each of these touchpoints and what steps are required of them?
Getting visibility over your processes is the first step to optimizing them. Once you have a clear picture of what is being done, you can then look at even simple automations that can eliminate manual handling and delays that come through unnecessary interactions. Consider the effectiveness of the tools you are using and whether there may be a simpler, cleaner or more effective solution.
Recognize the environment
The Formula 1 Grand Prix circuit spans the world and every stop offers its own unique challenges. In Malaysia and Singapore teams have to deal with temperatures routinely topping 100 degrees Fahrenheit with uncomfortably high humidity. In Dubai and Bahrain there is sand everywhere, even in the most well-maintained garages. At Silverstone in the UK rain is likely to be an issue more often than not. Each of these factors impact how the team performs and what is likely to be required of them.
While few businesses need to relocate every month, many enterprises do have multiple regional operations and different products, services, or functions across the wider organization. It is important to recognize these distinctions and find ways to work with them, while still striving for efficiencies in the way the business works.
Standardized processes ensure that the same function is performed the same way by each team that is required to fulfill it. They allow companies to implement global improvements, scaling the efficiencies from one site or team across others and ensuring compliance and conformity to established standards.
Where regulations or legislative requirements differ, however, or systems are either unavailable or require additional features, there needs to be room to adapt. Process variations need to be developed carefully to account for these distinctives, while still holding true to the core process flow wherever possible. They need to be recognized as necessary, but managed intentionally to ensure conformity and their support of the overall goals.
Know who is responsible
There can be twenty or more people in a Formula 1 pit crew, each with a dedicated function. The front-right first tire carrier is responsible for removing the old tire from the front-right corner of the vehicle as soon as it comes to a stop. That is it. They may have responsibilities in the wider garage throughout the race, but their core job is entirely to efficiently remove that one tire.
It is not likely that your business will have specialists to the same degree, but it is still vital that people know the role they are required to play. Imagine the chaos in the pit lane if the crew tried to decide which task they would do as the car screeched to a stop in front of them. Your processes should clearly indicate who the stakeholders are and who is responsible at each step.
As activities come due, ideally the responsible parties will be notified through automated workflows, and there will be no confusion about who to hand off to for the next step. Clarifying each function and assigning it to the right people ensures that there will be no bottlenecks as teams debate whose job it is to progress the activity.
Know the goal
Specialization allows for excellence in a field, but it should not distract from the strategic purpose of a business. If you ask a member of a pit crew what it is they do, they will tell you that they win races. While their function may be to remove a tire or wipe the driver’s visor, they understand how that contributes to the greater goal. They are part of a race team and their actions and responsibilities actively contribute to the outcome on race day.
Good communication around process ownership allows your business teams to gain the same perspective. By actively sharing stories of success and engagement, employees are encouraged to be part of continuous improvement efforts and see the impact they can have on the organization’s performance. Customer feedback and positive reinforcement from every level of management will ensure staff understand the part they play in the bigger picture and build enthusiasm for winning races, not just changing tires.
Fine-tuning the engine
Formula 1 pit stops are decided in the hundredths of a second and millions of dollars are spent on ensuring every moment of that time is optimized. While your business may not require the same level of precision, that focus on clarifying processes and efficient execution can still reap rewards that will put you ahead of the competition, and ensure you spend every minute you can on track to success.
Task mining – unlocking new possibilities in process optimization: Industry report 2025
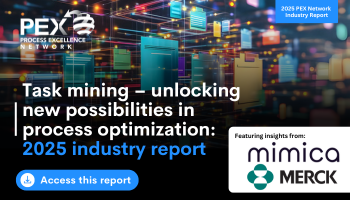
Task mining is experiencing robust growth, driven by the increasing need for process optimization and automation across diverse sectors. The market, estimated at US$2 billion in 2025, is projected to exhibit a compound annual growth rate (CAGR) of 25 percent over the next eight years, reaching an impressive $10 billion by 2033, according to Market Report Analytics.
Download this report to explore the task mining landscape and learn how it unlocks new opportunities in process optimization!
Download Now