The increasingly important role of process in health and safety
Discover two top tips for removing the anxiety of health and safety compliance
Add bookmark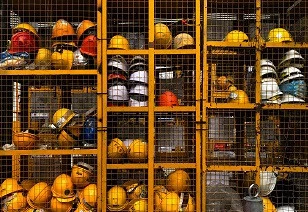
According to the International Labor Organization, there are approximately 6,000 occupational deaths every day. Their research shows another 374 million non-fatal, work-related accidents each year, every one of which results in at least four days of absence from work. The cost of this is monumental, reaching nearly four per cent of the annual global GDP.
Health and safety in the workplace is a significant issue as those numbers attest. The human cost and the burden of unsafe work practices on businesses is too high to ignore. Yet, health and safety remains a chore in most organizations, frequently viewed as an administrative headache to be endured rather than a key function of a healthy company.
That is not to say that it is being ignored. The International Organization for Standardization (ISO) developed ISO 45001 in 2018 to provide a framework for businesses to manage their health and safety systems.
In 2020 it added ISO/PAS 45005 to support managing the Covid-19 response. Certainly, the global pandemic has made everyone more conscious of health and safety both inside and outside the workplace, but how can an organization effectively lift them both out of uninspiring workshops and achieve ISO levels of management?
Do not run the risk of ignoring health and safety
Health and safety falls under the category of risk management in most businesses. As such, the cycle for managing it is the same as any risk: First the risk is identified, then assessed for its significance. What could happen? How severe is the likely harm and how likely is that to happen?
Once the risks are accumulated and assessed, it is up to risk managers and company executives to implement controls to eliminate, or at least mitigate, the potential harm. Any remaining risk is reassessed and recorded for ongoing monitoring.
Bear the two following points in mind to get a firm handle on risks related to health and safety.
Health and safety management is best viewed through the lens of being a process of its own
Part of the reason workplace safety is so maligned and under-resourced is that while it is touted as everyone’s responsibility, more often than not it is no-one’s direct duty. At best, it is delegated to a few individuals with limited resources.
Well-managed processes appoint stakeholders and champions, but invite everyone who participates in the activities to take an active part in ensuring it is as effective and efficient as possible. This is the core of continuous improvement, and when the task of identifying, quantifying and controlling risks becomes embedded in everyone’s daily duties, there is more chance of buy-in and engagement.
It also ensures that the process is followed. Where risks are identified, such as a power lead running between desks or a factory plant that does not meet compliance requirements, they are assessed then acted on. Having identified hazards does not contribute much to safety until those are isolated, eliminated or otherwise managed. By following established protocols your organization can make sure corners are not cut and the process is adhered to.
Processes contribute to health and safety through the controls themselves
With risks identified and ranked, numerous controls need to be established to reduce the potential harm. These could be anything from replacing equipment and revising work methods, to adding warnings and providing personal protective equipment for staff. Whatever the decided measures, the best way to ensure they are effective is to embed them in your processes.
Every control your health and safety risk management requires will tie to something your teams do. Those actions, decisions and procedures need to be captured and mapped in a way that makes them easy to find and follow for the people who execute on them. The more business processes you capture, the more capacity you have to manage those activities and actions performed in the everyday functions of your business. Where health and safety measures need to be implemented in a workflow, having an existing process available makes it easier to pinpoint where to make changes and ensure they are followed.
Take the headache out of health and safety
Health and safety is an essential part of any business, but it does not need to induce anxiety. Standards like ISO 45001 are not unreachable benchmarks for multinationals either. They are simply frameworks and expectations that can help you shape health and safety management.
By building processes around your risk management and embedding health and safety practices in your existing processes where those risks identify the need, your organization is already well on the way to meeting those standards and being a better workplace for everyone.