HelloFresh’s OPEX journey to efficiency and waste reduction
How HelloFresh reduced food waste by 50 percent
Add bookmark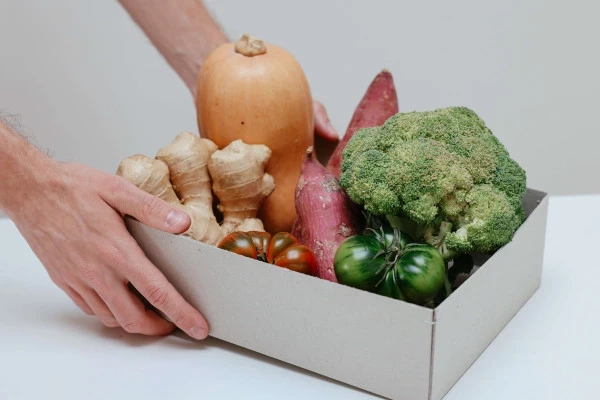
In an era defined by competition, the pursuit of operational excellence has never been more crucial. Studies show that organizations embracing OPEX experience a 10 percent reduction in costs and a 15 percent increase in revenue growth on average. As the business landscape becomes increasingly dynamic, the ability to streamline processes, enhance efficiency and strategically leverage methodologies like Lean Six Sigma becomes a non-negotiable factor in sustainable success.
At PEX Network’s recent All Access: Operational Excellence event, Abhishek Bhasin, national operational excellence manager at HelloFresh, delved into the meal-kit giants’ journey towards achieving operational excellence to improve efficiency and reduce waste, shining a revealing light on navigating challenges to forge a future of heightened productivity and competitiveness.
A culture of continuous improvement
HelloFresh prioritizes a culture of continuous improvement at all levels of the organization, something it has achieved through several key strategies, Bhasin said. “Firstly, it’s with leadership commitment, where leadership emphasizes the importance of its [continuous improvement] role in day-to-day operations and staying competitive according to the market dynamics.” This is a “top-down” approach where buy-in from leadership extends “all the way down to associates on the floor,” Bhasin added.
This helps in overcoming resistance to change, and educating associates on the floor about how operational changes will improve their day-to-day efficiency is very important, he said. “We were able to spend time with our associates and have them talk about what they are seeing,” Bhasin said, giving them the opportunity to share feedback on the changes they wanted to see and his team the chance to see if they could be implemented. This helped associates “feel included” in the operational excellence and change management journey HelloFresh embarked on, he added.
This engagement process – which included simulations and breakout rooms – was handled internally with a training team working directly with HelloFresh employees who benefitted from the opportunity to voice their opinions. “It’s an “egoless” environment where we listen to everyone and see what they bring to the table. It’s really important that everyone plays an equal role across this journey – from leadership to floor level,” Bhasin said.
Watch Abhishek Bhasin explain how HelloFresh is improving efficiency and reducing waste using Lean Six Sigma.
Using Lean Six Sigma to drive efficiency
HelloFresh has used Lean Six Sigma approaches to help drive efficiency, with the DMAIC (Define, Measure, Analyze, Improve and Control) model a prime example. This was related to the overproduction of food products that created significate waste, Bhasin said. “We defined the problem – that we were overproducing on a weekly or monthly basis – and then we measured the challenges we had and analyzed the areas of improvement based on a set of metrics.”
Once at the improvement phase, HelloFresh defined why overproduction was an issue and identified what needed to change to tackle the issues. The control phase saw the company bring waste down by 50 percent, Bhasin said. “This was one of the great experiences I’ve had working on a project where we implemented Lean Six Sigma methodology, and the same methodologies could be applied across other functions as well.”
However, such an endeavor is not a “one-day thing” he added, and it needs to repeat “day in, day out” to see value, change the status quo and improve process efficiency. “It’s not a sprint, it’s a marathon.” In terms of timelines, it took the company around six months to address its overproduction and waste problem, which is something it continues to assess and improve over the long-term, Bhasin said.
Prioritization and data-driven decisions
Prioritization is a key element of an operational excellence journey, and HelloFresh considered two key factors to focus on its chief goals of improving operational efficiency, Bhasin said. “First, we had to consider the cost issues we had and the impact on our physical product waste. Second was the impact on operational efficiency.”
Data-driven decisions played an integral role in HelloFresh’s efforts, Bhasin added. “When we are deciding on the KPIs [key performance indicators], what we are looking for are our overarching business goals and objectives, and then our priority based on areas of improvement.”
HelloFresh set a data-driven dollar value in relation to wastage and waste reduction, Bhasin said. “KPIs need to be SMART – specific, measurable, achievable, relevant and time-bound.” Once KIPs are set to achievable and relevant targets, they can be improved further by challenging the status quo, he added.
Three steps to operational excellence
There are three key steps to starting an operational excellence journey, Bhasin said. “First is communication – that is a key factor. The more you talk to key stakeholders the more information and ideas you get about the process or whatever you are planning to fix.”
Next is collaboration – avoiding silos and working with various teams and departments to achieve your goals. “You need an open mind; accept ideas and brainstorm on different things. You may not have experience in a lot of things, but you can get it once you start talking and involving yourself with others.”
Third is to have confidence in what you are doing and trying to achieve, Bhasin said.
Registration for next year’s All Access: Operational Excellence is open now!