7 process mining myths debunked
The truth was set free at the recent PEX Network All Access: Process Mining and Process Intelligence webinar series
Add bookmark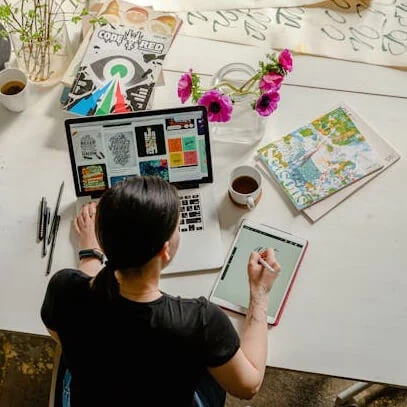
Process mining is at an interesting crossroads and has the potential to transform organizations, but first leaders need to understand its value. To start, process mining is a technique that allows business people to track processes with event logs. This provides the opportunity to identify bottlenecks, recognize ways to improve efficiency and help people become more productive. More recently, process intelligence has done the same by leveraging data analytics and artificial intelligence (AI).
Don't miss any news, updates or insider tips from PEX Network by getting them delivered to your inbox. Sign up to our newsletter and join our community of experts.
In early March 2024, the PEX Network community gathered for the All Access: Process Mining and Process Intelligence webinar series, where thought leaders and audience members drew the same conclusion: process mining is most effective when people remain at the core of the business and they commit to continuous improvement.
READ: 9 process mining obstacles and how to overcome them
Myth 1: People don't matter in process mining
Virtually all the speakers at the webinar series brought up the fact that process mining efforts only work if people are on board. Many hear about these efforts and worry if those tracking processes are going to eliminate the people in the name of efficiency and cost cutting. Change management and nurturing relationships with employees goes a long way to getting the most out of process mining.
"Maybe there's another dimension when it comes to the people running the process, because sometimes they just fear the automation. They [feel they] are maybe losing control over the process," said Jean-Marc Erieau, director of process mining and execution management at MANN + HUMMEL Group. "That's why it's sometimes an easier step to make a semi-automated process that you just generate some tasks."
The bottom line is that if the organization's employees and leadership do not buy into process mining (or fear it) the benefits will never be realized. Therefore, the people not only matter; they might matter the most.
WATCH: Are you up to speed on process mining?
Myth 2: Automation is the solution to all problems
Yes, new technology is making automation easier and more accessible than ever. About 50% of the audience said process mining accelerates automation and optimizes projects when considering it as part of a company's digital transformation journey. But it is not a panacea. Erieau and his fellow panelists agreed that those in charge of process mining should use the information gathered about processes to make thoughtful decisions that take into consideration many factors. Sometimes, less automation (not more of it) will be the answer. Leaders must consider each situation on a case-by-case basis.
"Process mining can support the acceleration of automation projects in multiple ways," said Elham Ramezani, leader at KPMG Centre of Excellence for Process Mining. "What is the degree of automation currently? Where does it make sense to automate? Where will we get the most gain because you want to automate?"
Perhaps, the message was clearest when Urszula Jessen, process mining expert at ECE Group Services GmbH & Co. KG, spoke:
"There is one thing they should ask themselves, 'Why is there an automation need at all?' Is it a real need for automation? Or maybe it's integration? Maybe there's something wrong with that process itself," said Jessen. "You will have to do some kind of change management to the process or integrate the systems between them because if they automate just to automate or automate a crappy process, the automation will break you."
Myth 3: Different parts of a process must happen in silos
Often, different departments handle different portions of a particular process and until recently they have not communicated with each other. Kya Shoar, director of product marketing at Celonis, pointed out that working without transparency among the different groups and failing to see the process from start to finish could result in shortsightedness. However, process intelligence is changing all that.
"So, how is process intelligence transforming process excellence? Well, process intelligence gives enterprises a common language to achieve their enterprise goals...This is where process intelligence comes in as the connective tissue of the enterprise," said Shoar.
"It gives you real time process observability by capturing every moment of every in-flight process end-to-end across the enterprise and going beyond just static transparency into what's happening in your process. So this intelligence enables you to orchestrate your processes. It provides the right decision support for your teams to take the right actions, but also for you to trigger individual workflows or process steps based on the intelligent process insights that you have."
WATCH: Prepare your business for the next era: Introducing process intelligence
Myth 4: "Set and forget" is the path forward
Process excellence professionals probably know this one is a myth, but many outsiders looking in believe perfecting a process is a one-and-done chore. It is more than that. Processes – and maintaining efficiency and productivity – is continuous. It depends on the people to keep up the momentum and attenton to detail.
"We can change process. We can change the technology, but we also need to ensure the people are changing as well," said Jack Moloney, senior director, SAP business process & governance architecture. "Without the people, we're not going to be able to take advantage of a lot of those changes within our technology and our business processes that we would have otherwise wanted to achieve."
WATCH: Business transnformation and change management in the digital age
Myth 5: The motivation for process mining is different for everyone
This might shock people because each industry and function is unique, so it seems plausible there would be different reasons for investing time and money into process mining. However, Maxwell Smith, senior director of product marketing at iGrafx, reminded the PEX Network community that every organization has the same goals.
"How specifically this happens does vary between industries, but at its core there are pretty common goals for businesses," said Smith. "You want to improve productivity, which is getting more done with the resources you have or building better products with the resources you have. You want to reduce costs, which means you want to keep the volume pace and quality stable as you're decreasing or scaling back investment. Often, these two go hand-in-hand. I'm sure you've heard do more with less, particularly in the macro-economic environment we're in. The third, sometimes forgotten, focus is ensuring compliance both with internal policy and external regulation."
WATCH: Upleveling from process mining to true process intelligence
Myth 6: Data solves all process challenges
Nowadays, business leaders have access to more data points than anyone could have imagined even just a few years ago. Making sense of the data, translating it and leveraging it for long-term strategy and planning is an art. Having the data alone is meaningless.
"People love to collect data. We've been doing it for years on clipboards and with servers and sensors and all this kind of stuff. We don't know what to do with the data," said Michael Muilenburg, co-host of the Voices of Manufacturing Podcast. "So, it sits around collecting dust and then we'll grab somebody who maybe doesn't even have the skills and say, 'Go, analyze all that data,' and they're using dusty old data. They don't know what to do with it. They spent all this effort, creating graphs and charts and analytics, and there's no business result."
WATCH: Building a culture of continuous improvement through process mining and stakeholder involvement
Myth 7: No room for mistakes in process mining
Obviously, the purpose of process excellence in general is to improve how organizations get things done. The idea in process mining is to remove errors and not add them. However, in experimenting and figuring out the best paths forward, people must take risks. Sometimes, things don't work out as planned – and that's more than all right. Sometimes, those mistakes lead to greatness.
"I think that it is important to celebrate the trailblazers," said Ricardo Henriques, transformation leader & business automation professor at Católica Lisbon School of Business and Economics. "You must give them space to fail but try to fail fast."
Failing is the first step to succeeding in process mining – and much of life for that matter. The panelists who joined All Access: Process Mining and Process Intelligence share different perspectives and approaches to process mining. They all agreed, however, that people must be given space to learn, understand and value process mining as a means for continuous improvement.
PEX Report 2024 global state of process excellence
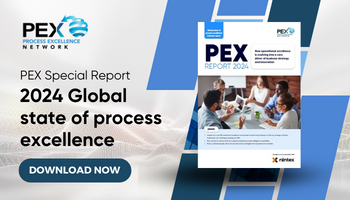
PEX Network's annual report reveals the current state and future trends of process excellence. Based on a study profiling hundreds of global process excellence leaders, the report provides insights on how to leverage innovation, generative AI, and process intelligence to achieve operational excellence, customer-centricity, and organizational growth. Download your copy of the PEX Report 2024 today and benchmark your process excellence journey against your peers.
Download Now