How to control ineffective workflows in manufacturing industry
Learn how manufacturing industry facing challenges since covid-19 pandemic and optimizing processes is beneficial for workflow automation & smart manufacturing
Add bookmark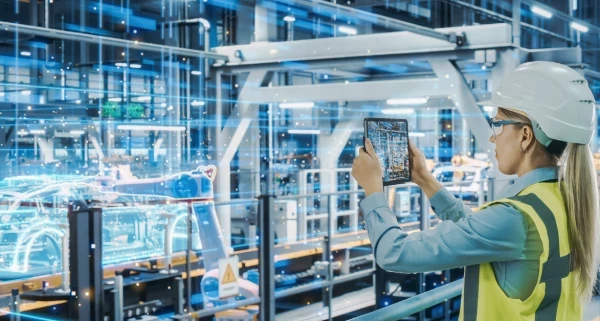
What are the benefits of optimizing processes?
The landscape of the manufacturing industry is changing in ways that may be permanent. The Covid-19 pandemic is largely at fault since it disrupted many aspects of the industry from supply chain to worker availability as a result of travel and shipping restrictions.
Optimizing processes can help manufacturing companies minimize the impact of the industry’s changes such as increasing competition. Organizations can make adjustments to their operational strategy or leverage workflow automation to continue to drive operational excellence (OPEX) in its birth place in 2022 and beyond.
This PEX Network report features insights from industry experts from the likes of Procter & Gamble, Campbell Soup Company and E.T. Browne Drug Co. It looks into why driving process improvement in manufacturing is becoming more difficult, the areas that need to be addressed and offers potential solutions.
“Anything that can accelerate ‘time to capable’ for machine operators would be welcomed with open arms. Current new hires come with zero previous machine operation, troubleshooting or maintenance experience.”
Hank Ward
Operational excellence lead at Campbell Soup Company
Managing the disruption of the Covid-19 pandemic two years on
The manufacturing industry is only becoming more competitive with the US manufacturing market alone having grown at an average CAGR of 1.4 percent between 2017 and 2022 and revenue expected to reach US$7.94tn in 2022.
The competition is forcing manufacturers, who are competing for the same customers, to reconsider the way they work and develop new strategies to survive in a more competitive environment.
One industry survey found that the pressure to stay ahead of competition is affecting the majority of manufacturers, with 88 percent agreeing that they have changed their business model in order to better compete under current market conditions.
The manufacturing industry has been hit hard by the Covid-19 pandemic, exposing vulnerabilities in global supply chains.
Manufacturers are highly reliant on effective supply chains in order to keep materials flowing in and out of plants as quickly and as cheaply as possible. When the Covid-19 pandemic hit, many manufacturers were unable to receive materials from suppliers located abroad. This is still an issue today, according to Hank Ward, operational excellence lead at Campbell Soup Company.
“Supply chain [is where the Covid-19 pandemic has had the biggest impact], we cannot get the ingredients, packaging supplies and machine parts nearly as easily as pre-pandemic,” he says.
Operational adjustments have also been necessitated by the pandemic. Manufacturers had to take steps to adjust working processes to ensure proper hygiene and safety for workers, adding further strain to manufacturing operations due to the need for the addition of new hygiene and safety processes that workers would have to learn.
Complex or inefficient workflows
Complex or inefficient workflows can slow the pace of production as employees can get caught in long-winded processes instead of making the products their company sells.
E.T. Browne Drug Co. was operating with an inefficient process for the design and redesign of packaging and labels for its products. It involved manual review of new designs by numerous departments across the business including research and development, marketing, legal and compliance and manufacturing.
Documents were sitting on managers’ desks for weeks. This was a major issue, as it delayed time-to-market for the business’ products, which was highly damaging to revenue.
The next section of the report will discuss how operational processes such as supply chain or training processes can be optimized.
The need to optimize operational processes
Improving inefficient workflows
Ensuring a smooth flow of materials, parts and other necessary inputs is critical for manufacturers. For this reason, Campbell Soup Company’s Ward believes that supply chain optimization should be the number one area of focus for manufacturing organizations in 2022.
“Supply chain is the key process organizations need to focus on to enhance operations. We need to work on getting the inputs needed, where we need them and when we need them.”
Marc Winkelman, global director for IWS manufacturing excellence at Procter & Gamble, agrees with this assertion and told our sister portal Pharma IQ: “The challenges for pharma are the same as for all other manufacturing companies: how to be faster, better, cheaper, compliant and sustainable. We need to deliver supply chain results that beat the competition.”
An example of driving OPEX through supply chain optimization comes from Nike. Chris Hill, former process excellence manager at the global sportswear company, offered insights in The PEX Report 2022: Global state of process excellence into the steps it takes to ensure supply chain excellence.
The business developed a tool that utilizes a data solution to give a new level of visibility over supply chain operations so that issues or delays can be detected and identified according to Hill.
“The tool is a visual basic for applications data solution relying on code to eliminate the manual tracking, aggregating and reporting of shipment data through a standardized form, with encoded logic to automate the aforementioned tracking and reporting process in real time,” Hill explained in the report.
Data is shared throughout the business via a centralized platform, which is in turn integrated into quality assurance processes. This allows the business to determine what projects to initiate to improve shipping performance. The initiative launched by E.T. Browne Drug Co. saw similar success with regard to increasing the visibility and accessibility of packaging data across the business.
The business decided to automate its inefficient workflow for packaging design but came up against another challenge.
They needed to aggregate both numerical and visual data and content depicting the packaging and labels, which needed to be viewed by every department.
The business utilized the Nintex Workflow platform to develop a solution. It now allows every department to view the relevant files from a single source directly from notification emails on their computer or on their mobile devices.
Pieter Goes, vice-president of IT and business intelligence at E.T. Browne Drug Co., says: “We can pan and zoom into a label in Nintex Workflow to see details we would not have seen in a PDF. We do not waste time searching for the right files, do not experience pauses or errors in workflow, do not have to track down workflow status. The review process just works much faster and more reliably than before.”
The solution cut the process time in half and generated a predicted return on investment (ROI) of 5,005 percent (US$29mn) over the five years following implementation.
Through the use of a centralized platform like this, E.T. Browne Drug Co. Has eliminated the need for plug-ins, downloads or special applications such as Acrobat or Adobe Illustrator for viewing files. This has also eliminated the need to send files around the organization. By drastically shortening the length of this process, the business has improved its time-to-market and no longer has to worry about losing sales as a result of it.
Focusing on training processes
Supply chain issues have been compounded by the decrease in the number of available workers across the globe. At first this was a direct result of the pandemic, with workers off sick or forced to remain home as a result of government-enforced lockdowns.
Following this, the large swathe of resignations and retirements that many industries experienced has resulted in a skill shortage. There is an influx of, according to Ward, “zero-skilled talent entering the workforce” who need to be fully trained.
Due to the impact of the pandemic on the level of skilled talent available for manufacturers, optimization to training and education processes should be a key priority for improving speed and efficiency of production. This is the area where Campbell Soup Company’s Ward sees the most value coming from.
“Anything that can accelerate ‘time to capable’ for machine operators would be welcomed with open arms,” remarks Ward. “Current new hires come with zero previous machine operation, troubleshooting or maintenance experience.”
Procter & Gamble’s Winkelman believes that one of the best strategies for accelerating the training and development of workers is to make manufacturing operators the equipment owners.
Manufacturers should encourage operators to master the standards of the equipment and their work processes and give them responsibility for the day-to-day operational decision-making.
“During the pandemic, we trained our staff so well that with or without leadership on-site in P&G’s factories, they were able to continue running as before the pandemic restrictions,” Winkelman notes.
The next section of this report will look at how digital technologies can drive operational excellence in manufacturing.
The value of smart factories
The concept of a smart factory, or digital factory, is derived from smart manufacturing and industry 4.0, two other trendsetting, industry optimization initiatives. It is an extension of the industrial Internet of Things (IoT) and involves interconnecting all plant resources such as machines, robots and equipment and supporting them with computing power.
Digital manufacturing generally involves deploying various types of sensors across the factory floor and embedding them into machinery to generate a real-time flow of data that reports on the activity and functioning of every part of the factory. Traditionally, such information was kept locally on individual devices and only analyzed to assess the cause of equipment failures.
Digitization took this a step further, allowing data to be centralized and stored on shared systems where it could be compared against data from other parts of the factory upon analysis.
Smart factories go even further than this through the continuous analysis of real-time data that allows for visibility over what is happening. Such data also affords transparency with regard to why it has happened and even goes as far as predicting what will happen and embedding automatic responses into plant machinery for when it does.
The Covid-19 pandemic put home appliance manufacturer Whirlpool’s smart factory to the test. The business found that the high level of visibility it had over factory processes from the sensor arrays allowed remote monitoring for its operators.
Workers tasked with monitoring equipment or production cycles could perform their jobs just as well without even being present in the factory.
Another big win for Whirlpool’s smart factory during the pandemic came from the application of augmented and virtual reality. By combining these technologies with the extensive plant data, the business was gathering, it was able to have workers visually review and redesign workstations, working cycles and line layouts from their own homes.
“The challenges for manufacturing companies are how to be faster, better, cheaper, compliant and sustainable. We need to deliver supply chain results that beat the competition.”
Marc Winkelman
Global director for IWS manufacturing excellence at Procter & Gamble
Conclusion
With the manufacturing industry only growing more competitive and with the lessons that have been learned following the pandemic, there has rarely been a better time for manufacturers to begin considering how they can drive OPEX.
Manufacturers will need to take steps to mitigate the ongoing supply chain disruption the pandemic has caused by improving visibility over shipping through the aggregation and centralization of data. They will also need to take steps to ensure that they are able of developing skilled workers in-house, as the constant availability of skilled hires is not something manufacturers can rely on any longer.
Businesses can leverage workflow automation to iron out inefficiencies and delays in their processes. One of the major advantages of this is the improvement of time-tomarket which, in such a competitive environment, could be the difference between losing or keeping sales.