OPEX Top 10 Transformational BS (Bogus Statements): PMO-Driven Programs
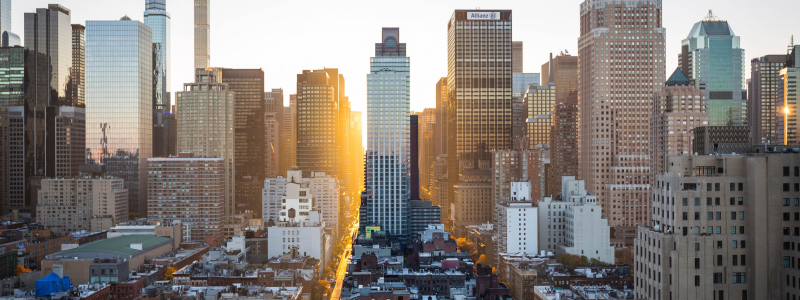
In the lead up to the 5th annual OPEX Week Europe summit, the official event blog will become home to some of the industry's most informed and influential voices. In this blog post, Anthony Shingleton, VP Business Development EMEA at Simpler Consulting (an IBM company) explores one of the many OPEX 'urban legends'.
In the run up to Simpler Consulting's session at OPEX & Business Transformation Europe, “Breakthrough Next Generation Transformation: Simplify, Automate & Augment”, we felt it was time to look back on the past and dispel some of the most common statements we hear about transformation. Our first article was about “Change Fatigue”, our second about “Outsourcing”, today we look at “PMO-driven Programs” and the reason why so many fail to deliver results and why many executive teams no longer rely on them to make long lasting real change.
If you look at how little transformation deployment strategies have changed since the GE, Motorola, Allied Signal days you can sometimes wonder if the internet has really help spread best practice. Let me be clear: there is a time and a place for large PMO-lead and charismatic leader-led programs, so this article is not about dismissing this deployment strategy. This article is about responding to the change in the pace of change, i.e. the need to keep changing faster and more often.
The Problem
The “problem” with PMO-led programs is that they are not known for creating empowerment, long-lasting changes, culture changes or everlasting breakthrough performance year and after year. And why should they? By their nature, PMO-led programs are just big projects that have a tendency to be run by people with conventional Gantt Chart and/or Prince II expertise. Again, there is nothing wrong with these methodologies but let’s remember where they came from and see why they might not be able to satisfy the need for speed, agility and permanent change:
- Gantt Charting-based methodology comes from the production environment which was typically described as multi-variable dependent. This method focuses on efficient use of resources and planning activities over long periods.
- Prince II methodology came from the UK Government which recognised the need for standardisation and prescriptive operational procedures to ensure constant delivery across a very large employee base.
What both methods have in common (in a bad way) is that they both take time to:
- Setup the project management office (PMO) and team.
- Decide what needs to be done
- Agree on a transformation plan
- Document the transformation plan
- plan Document the transformation plan Get agreements from steering committees and executive teams
- Get agreements from steering committees and executive teams
There was time where the pace of change needed was sufficiently slow that one could afford this lengthy program initialisation time and speed of deployment. Sadly, this is simply no longer the case.
Both methods also operate, by design, under a “Command & Control” governance model which is report-driven and which requires multiple sign-offs.
Because they (try to) operate based on efficient use of resource and sign-offs they are often behind schedule due to pile up (inventory) of decisions to be made in steering committees that don’t meet up frequently enough.
Since Lean can be applied to any process, let’s do a quick and dirty waste analysis of PMO-Led programs using TIM WOODS, i.e. the 8 wastes of Lean. What we see is all 8 forms of waste, i.e.:
- Transfer (Items) of reports, emails, documents from persons to persons
- Inventory of reports, meetings, decisions awaiting action
- Movement (People) of Project Managers from place to place
- Waiting for things to happen
- Overproduction of activities and Gantt Charts revisions
- Over processing of reports and audits
- Defects in tracking, reporting, training or execution
- Standards missing, incorrect or incomplete
The Solution
By now you are hoping that there might be an answer or a better way to make change happen when your criteria includes the need for agility, people empowerment and everlasting double-digit yearly improvement. Rest assured, there is. Even better, the solution is industry or function agnostic. What’s it called? Simply “Project Flow”. Why? Because transformations are one-off processes where the value being created is through the flow of knowledge, decisions and risk. Find the least waste way to do this and you will quickly start moving away from Gantt Charting/Critical Path thinking and Prince II type thinking. Of course there is a little more to it, but this article is not about giving a full description, it is about recognising the need for change in how transformations are driven.
In conclusion, just like everything is changing faster there is no reason why transformation methodologies shouldn’t do the same. There comes a time when you just need to stop doing the same thing while expecting a different result (Einstein’s definition of insanity!). There is nothing in the 5 principles of Lean that says that this way of thinking cannot be applied to non-recurring processes (projects or transformations). You just need to think strategically and create standard work at sufficient strategic level so that anyone (yes anyone) can run a Transformation in the least waste way. The rest is just about scaling up!
If you’d like to know more about how we help organisations make outsourcing a success, then why not have a chat with us at OPEX Week Europe later this year.
Thank you for reading and feel free to provide feedback via email or LinkedIn.